RDL Coatings offers a wide range of metalized coatings including: Tungsten Carbide, Nickel Chrome, Stainless Steel, Aluminum, Aluminum Oxide, and Chrome Oxide.
We also offer a variety of polymer coatings such as Epoxy’s, PTFE, PFA, and FEP. All of our coatings can be sprayed at a variety of surface textures based on your needs.
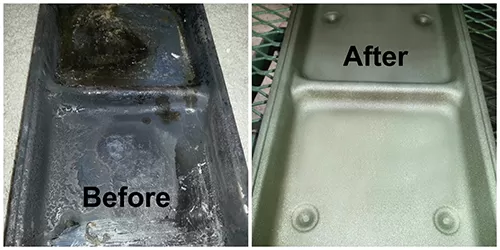
Wear Coatings
Accelerated wear issues can be crippling to production. It is the most common cause for equipment maintenance and downtime. Over time, every day mechanical and contact stress takes a toll on your components. As products travel over your equipment or when machine operators continually cut on the equipment, it is common for parts to get worn down and for deformations to occur which ultimately affects your product output causing inconsistencies and variation.
RDL Coatings offers a line of hard, durable, wear-resistant coatings which serve as a protective barrier over your parts; creating a hard surface barrier making your equipment resistant to wear and abrasion. Ultimately, our coatings extend the life of your components and greatly reduce the need for maintenance.
All of our coatings can be applied in a wide variety of surface textures based on your specific needs. They can be applied to both cylindrical and flat parts and bond excellent over Aluminum, Steel, Stainless Steel, and Carbon Fiber Substrates.
PROBLEMS SOLVED
- Wear
- Equipment Replacement
- Product Defects & Inconsistencies
- Shutdowns
COMMONLY COATED PARTS
- Rolls
- Shafts
- Plates
- Mandrels
- Guide Rails
- Tubes
- Chutes
Traction Coatings
Traction control is a critical element in production lines in order to optimize line running speed. When components lack grip, slippage issues can occur, drastically slowing down your line causing web interruptions and breaks. This results in product fall-out and reduces the overall functionality of components. Unlike traditional wrapping methods, applying a traction coating is a long-lasting, low-maintenance solution to this problem.
RDL Coatings offers a line of hard, durable, traction coatings that provide grip to pick your product up and push it along; optimizing line running speed. Since wear is an issue in the majority of traction applications, our coating is applied in two phases. First, a high quality, durable metal is thermally sprayed onto your part offering superior wear and abrasion resistance. Second, a specialty agent providing traction is impregnated onto the surface. This agent can be applied at various surface roughness textures and profiles based on your specific needs. These coatings can be applied to a wide array of both cylindrical and flat parts and bond excellent over Aluminum, Steel, Stainless Steel, and Carbon Fiber Substrates. These coatings have been found to have a significant impact particularly in the printing, paper, film, foil, and label industries.
PROBLEMS SOLVED
- Slippage
- Wear
- Equipment Replacement
- Product Defects & Inconsistencies
- Shutdowns
- Air Entrampment
- Tracking
COMMONLY COATED PARTS
- Feed Rolls
- Pull Rolls
- Anvil Rolls
- Fingers
- Guide Rollers
- Winder Drums
- Nip Rolls
Release Coatings
Products sticking in the production process is one of the top problems faced by manufacturers. To combat this, many manufacturers try wrapping parts in tape, sandpaper, and wax. The problem with this approach is that these products have to be reapplied frequently because they unwrap or get accidently cut by machine operators.
RDL Coatings has developed a line of non-stick coatings that offer a wide variety of surface texture and release properties based on your specific needs. These coatings are applied in two phases. The first provides a hard base, protecting your substrate from wear. Second, a release agent is applied which provides the perfect texture to allow your product to glide smoothly over it. Your parts stay cleaner and build up and web snagging is highly reduced resulting in longer production runs and less machine downtime. Our customers report both an increase in productivity and a significant reduction in maintenance costs.
PROBLEMS SOLVED
- Sticking
- Build Up
- Web Snags
- Shutdowns
COMMONLY COATED PARTS
- Idler Rolls
- Pull Rolls
- Pans
- Guide Rails
- Drive Rolls